Pourquoi utiliser la méthode du Lean management au travail ?
Pourquoi utiliser la méthode du Lean management au travail ?
Sommaire :
- Quels sont les fondements du Taylorisme ?
- L’histoire du Lean Management
- Quelles sont les principes du Lean Management ?
Pourquoi faire du Lean Management
4. Quels sont les étapes pour mettre en place la méthode du Lean Management ?
5. Quel est le principe du juste-à-temps ?
Qui a inventé le juste-à-temps ?
6. Puis-je appliquer la méthode dans mon entreprise ?
Nous rencontrons tous des problèmes d’organisation et de gestion dans nos entreprises et c’est pourquoi, il faut souvent repenser le processus.
Le problème, c’est que la démarche de reconsidération prend du temps et n’est pas des plus facile à mettre en œuvre. Avec les années, il arrive que les pratiques et les habitudes mises en place dans l’entreprise, n’ont pas bénéficié d’un suivi régulier, alors que dans l’idéal, il le faudrait afin que le processus évolue de manière fluide, claire, tout en prenant en compte le bien-être des collaborateurs.
Pour vous faire un exemple, vous êtes responsable HSE (hygiène, santé, environnement) dans une entreprise agroalimentaire qui existe depuis plus de 50 ans. On vous demande de repenser le processus afin de supprimer les problèmes de retard et de coût dans le but de satisfaire au mieux le client final. Ce que vous devez faire en premier lieu, c’est la représentation du processus utilisé à l’instant T, analyser à quoi sert chaque élément et identifier les personnes chargées de chaque étape.
Mais avant de vous dévoiler la suite, on vous invite à découvrir une ancienne méthode dite “arbitraire” : le taylorisme, qui ne considérait pas le bien-être des salariés dans son processus, en opposition au Lean Management qui en fait l’une de ses priorités.
1. Quels sont les fondements du Taylorisme ? (Frédéric Winslow Taylor)
W. Taylor, fondateur du Taylorisme en 1911, avait comme précepte organisationnel, l’amélioration de la productivité, intitulé “La Direction Scientifique des entreprises”. C’est au travers d’un meilleur contrôle de l’activité des ouvriers, qu’il voulait lutter contre la flânerie dans les ateliers en trouvant la meilleure façon de produire.
Pour ce faire, M. Taylor propose de s’aligner sur deux préceptes très similaires au Fordisme : La division du travail horizontale et vertical du travail, qui s’articule autour de la répétition des gestes, en séparant travail de conception et exécution. Et tout ceci, accompagnés d’une surveillance chronométrée.
Cette méthode a effectivement fait ses preuves en termes de volume de production, mais rend le travail des ouvriers particulièrement difficile, impactant directement la qualité de la production, ce qui vient à remettre en cause l’utilisation du Taylorisme afin d’adopter une vision plus sociale et humaine dans le processus.
2. L’histoire du Lean (Taiichi Ohno)
Après la guerre de Corée, dans les années 1950, avec une demande de plus en plus accrue, le Japon n’arrive pas à faire face à la concurrence internationale du secteur automobile. Pour répondre à ce problème, deux ingénieurs japonais, Taiichi Ohno et Eiji Toyada de l’enseigne Toyota, ont développé, leur propre système de production (TPS) qui permet de réduire les processus n’ayant aucune valeur pour le client final, c’est-à-dire respecter ses exigences en matière de coût, de qualité et de délai tout en garantissant un environnement de travail optimal pour ses salariés en mettant en pratique des méthodes visant à supprimer sans attendre les éléments gênants dans le processus.
En faisant cela, Toyota a réussi à obtenir des améliorations significatives en termes de productivité, d’efficacité, de temps et de rentabilité.
Par la suite, la notion de Lean s’est petit à petit propagée dans les autres industries. Celle-ci a ensuite été enrichi par le “Lean Management Institute” autour de 5 principes de base de la gestion du Lean, communément appelés, les 5 Zéro qui vous seront présenté ensuite.
3. Quelles sont les principes du Lean management ?
Si une entreprise se porte bien, cela ne veut pas nécessairement dire que sa gestion interne est simple. C’est pourquoi, nous souhaitons vous présenter la méthode du Lean management qui, avec le temps, a su faire ses preuves.
Le Lean Management signifie “sans superflu” en anglo-saxon. Elle reflète exactement ce qu’évoque cette méthode, réduire les choses à l’essentiel et supprimer ce qui est inutile. Cette notion, créée par Taiichi Ohno, est connue pour s’établir dans une démarche BPC (Bien du Premier Coup), elle s’appuie sur la capacité des collaborateurs à faire remonter les informations et les difficultés rencontrées, de les hiérarchiser afin d’identifier les problèmes et de trouver des solutions. Cela implique de travailler sur une base de flux stables, avec des équipes formées pour évaluer les performances et les comparer aux premiers, dans le but d'améliorer continuellement le processus.
Pour expliquer cela de façon moins formelle et dans un cadre de référence, ce processus vise à optimiser le temps de production, sans valeur ajoutée (opération et transport inutile, surproduction…).
Le Lean est tournée vers un management permettant aux collaborateurs de travailler dans les meilleures conditions. L’objectif étant, l’entière satisfaction du client final ainsi que l’équilibre entre le bien-être des salariés, la qualité et l’efficacité de la production.
Pourquoi faire du Lean Management ?
L’instauration de cette méthode permet d’améliorer dans son ensemble et de manière continue le processus et la satisfaction des salariés qui se sentent tout de suite plus impliqués dans l’entreprise.
De ce fait, cela engendre une augmentation de leur motivation et du bien-être au travail, qui sont des facteurs permettant de maintenir la santé des salariés aussi bien sur le plan physique (moins de risques d’accidents, etc.), mental (éviter les dépressions, le burn-out, etc.) et relationnel (meilleure entente entre les salariés, etc.).
4. Quels sont les étapes pour mettre en place le Lean management ?
Le Lean Management est fondé sur 5 principes de base que vous devez suivre rigoureusement, dans une démarche de contrôle de gestion et de correction du processus.
#1 Identifier la valeur
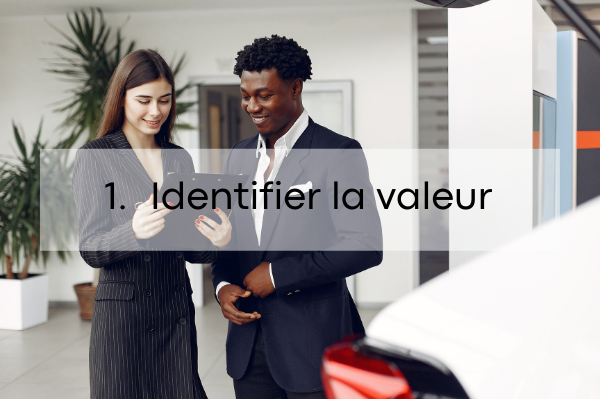
Vous devez, avant toute chose, identifier la valeur que vous souhaitez apporter à votre offre, pour ensuite la définir clairement.
La valeur de votre offre se trouve dans la manière dont votre entreprise va résoudre le problème du client, c’est-à-dire, la raison pour laquelle le client va se décider à acheter votre produit. Vous pouvez considérer que toutes les activités qui n’apporteraient aucune valeur à votre produit final, est a supprimé de votre processus de production.
#2 Cartographier la chaîne de valeur
Après avoir identifié la valeur de votre offre, il vous faut ensuite la cartographier. En appliquant ce précepte, vous serez capable d’évaluer les étapes non essentielles de votre processus.
Pour cela, vous devez dessiner votre chaîne de production en incluant les actions et les personnes concernées dans chaque étape, jusqu’à la livraison au client. Ce qui vous permettra d’avoir une vision d’ensemble et d’éliminer les étapes qui vous font tout simplement perdre du temps.
#3 Créer un flux de travail continu
Maintenant que vous avez cartographié la chaîne de valeur, assurez-vous que le travail de chaque salarié soit fluide. Prenez aussi en compte que chaque changement effectué peut mettre un peu de temps à être assimilé. Surtout, n’oubliez pas que vous ne faites pas tout cela seul, mais en équipe !
Pensez à diviser les tâches en petites parts pour que le travail soit moins drastique et plus facile à effectuer pour les salariés. Cela vous permettra de visualiser la dynamique globale de travail afin d’identifier plus facilement les obstacles dans le processus.
#4 Créer un système de traction
Votre équipe arrive désormais à exécuter ses tâches avec plus de facilité et moins d’efforts. Mais pour avoir la garantie que les actions mis en place soient stables, vous devez garder l’esprit ouvert en créant un lien avec vos salariés.
Dans ce cas de figure, vous devez rester à l’écoute et répondre aux besoins fondés de vos collaborateurs.
Pour prendre un exemple très simple, vos salariés ne prennent pas le temps de jeter à la poubelle les déchets engendrés par la production et préfèrent les jeter dans un coin par terre, en attendant. Ce qui a pour conséquence un débord sur les allées et occasionne une gêne lors des déplacements.
Dans un premier temps, vous devez identifier la raison de ces agissements en leur posant la bonne question : pourquoi jetez-vous les déchets par terre plutôt qu’à la poubelle ?
On vous répond que l’entrepôt est grand, que le point poubelle est trop loin et que cela fait perdre 10 minutes à chaque aller/retour.
Vous devez donc réfléchir à une solution et celle-ci pourrait être par exemple : la mise en place de sacs-poubelles à côté de leur poste de travail afin qu’ils n’aient à faire qu’un ou deux allers/retours grand maximum dans la journée.
Quel est le résultat ? Plus d’encombrement, un gain de temps, les salariés sont satisfaits et de ce fait, les clients le seront aussi.
Ce n’est qu’un exemple parmi tant d’autres et c’est de cette façon que vous augmenterez votre capacité de ressources, plutôt que de la gaspiller inutilement.
#5 L’amélioration continue
Si vous avez bien suivi les étapes précédentes, c’est que vous avez réussi à mettre en place votre propre système de Lean Management. Cependant, il ne faut pas vous arrêter là.
Lorsque vous mettez en place un tel système, il faut veiller à ce que celui-ci continu de s’améliorer et que vos collaborateurs continuent de contribuer à son avancement. Il faut que vous gardiez en tête que chaque processus est évolutif et que des difficultés peuvent survenir à tout moment, ce qui impactera directement ou indirectement le processus et engagera probablement des changements non désirés au départ.
Pour en revenir à ce que l’on disait plus haut, le fait d’établir un lien de confiance est important afin que vos collaborateurs se sentent investis et contribuent de manière constante à l’amélioration continue du processus. C’est en impliquant chaque niveau de la hiérarchie que vous pourrez obtenir des résultats durables, efficaces et performants pour l’entreprise.
Pour les responsables HSE ou RH, vous pouvez encourager vos équipes afin qu’ils se sentent plus investie. Vous pouvez, par exemple, mettre en place des réunions hebdomadaires afin d’échanger sur ce qui a été fait ou pas, et s’il y a eu des difficultés rencontrées. Cette méthode permet aussi d’alléger le travail de recherche sur les éventuels problèmes et d’optimiser quotidiennement le processus.
5. Quel est le principe du juste-à-temps ?
Le principe du Juste-à-temps est un outil reconnu qui vise à améliorer le processus de production, c’est-à-dire, produire le bon produit, au bon moment, en bonne qualité, à moindre coût et sans gaspillage.
Qui a inventé le juste-à-temps ?
Également appelé la méthode des 5 Zéros, elle a fait son apparition dans les années 50 et, sans surprise, a été développée par Taiichi Ohno. Bien qu’elle soit née il y a longtemps, elle est, de nos jours, très fréquemment appliquée en entreprise, notamment dans les secteurs industriels.
D'ailleurs, si vous êtes responsable HSE, on vous recommande de suivre cette méthode qui intègre des valeurs éthiques et environnementales à ne pas négliger.
-
Zéro délai
L’objectif du Zéro délai est de supprimer complètement le temps perdu entre chaque étape du processus de production afin de respecter les délais et de livrer le produit au client dans les temps impartis.
Ce qui revient à prendre en compte les étapes du Lean Management visant à identifier pour mieux supprimer les phases inutiles au processus.
Quel que soit le secteur, la réactivité de production d’une entreprise, reste l’un des facteurs de compétition essentiels pour les clients à ne pas sous-estimer.
-
Zéro stock
Pensez que les stocks ont un coût, puisque ce sont des actifs immobilisés et qu’il est nécessaire de les entretenir, de les stocker. Ils peuvent parfois même être dégradés ou volés.
Les entreprises tendent de plus en plus à fonctionner avec un flux de production tiré par rapport à la demande, ce qui permet d’éviter justement la surproduction. C’est pourquoi, on parle plutôt de stock minimum en travaillant avec juste ce qu’il faut pour anticiper les aléas.
Il est évident que si vous continuez à produire alors que vous avez déjà atteint un niveau de stock conséquent, cela peut devenir rapidement problématique. Vous fabriquez des produits que vous n’êtes pas sûr de vendre et s’ils ne se vendent pas, vous allez devoir les garder. Et si dans un temps imparti vous ne les vendez pas, ils peuvent se dégrader, vieillir et finir par ne plus correspondre aux normes de mise en vente sur le marché.
-
Zéro papier
Auparavant, la bureaucratie était déjà considérée comme une complication alourdissant les processus.
À notre époque, ce principe est d’autant plus important avec les préoccupations écologiques, en l’occurrence avec la nécessité de sauvegarder les forêts. De plus, avec les évolutions en termes de technologie et l’accès aux moyens numériques, nous sommes capables de stocker l’information sans avoir à imprimer.
Le Zéro papier vient d’aujourd’hui à repenser les processus de manière immatérielle et de faire en sorte que les documents de références soient principalement stockés de manière numérique et de n’imprimer que lorsque le besoin s’en fait réellement ressentir.
-
Zéro défaut
Les problèmes de surcoût important se trouvent dans les défauts de production, la plupart du temps, cela nécessite de recommencer le travail, d’allonger ses journées, de gérer les retours, etc. Mais c’est aussi le risque de perdre des clients parce qu’ils ne sont pas ou plus satisfaits.
L’objectif du Zéro défaut est de détecter les anomalies afin de les résoudre à leurs sources. Plus les problèmes seront identifiés rapidement, plus il sera facile de les résoudre.
C’est comme si vous procrastiniez le traitement de vos papiers administratifs. Et quand vous vous décidez de vous en occuper, vous vous retrouvez avec un tas de papier à traiter pendant plusieurs jours.
Tout compte fait, le zéro défaut vous démontre que traiter les difficultés avant même qu’elles n’apparaissent vous permet de gagner un temps considérable.
-
Zéro panne
Dans le même principe, la notion de Zéro panne a pour objectif de détecter les dysfonctionnements des machines avant même qu’ils ne se produisent. Il est donc primordial de traiter les anomalies liées aux outils de production afin d’éviter au maximum les pertes.
C’est pour cela, qu’il vous ait fortement recommandé de créer du lien avec vos collaborateurs en faisant le point régulièrement sur leur travail et vous intéresser aux difficultés qu’ils auraient rencontrées au cours de la semaine précédente pour trouver une solution au plus vite.
N’hésitez donc pas à les motiver à faire remonter les anomalies dès qu’elles se présentent plutôt que d’attendre le dysfonctionnement total des machines.
6. Puis-je appliquer la méthode du Lean Management dans mon entreprise ?
En principe, il n’y a aucune raison que vous ne puissiez pas utiliser la méthode du Lean Management dans votre processus d’amélioration continue.
Il est tout à fait normal de vouloir intégrer une approche qui permettrait à votre entreprise de bien fonctionner.
Vous pouvez appliquer cette méthode dans votre entreprise, à la condition d’être conscient que celle-ci requiert une régularité, relevant d’un ajustement permanent, quant à l’évolution de votre projet.
Le Lean Management est un état d’esprit. Et pour mettre en pratique cette méthode, vous devez vous mettre en tête que le chemin pour y parvenir se fera progressivement.
Pour cela, je vous donne un dernier petit tips. Appuyez-vous sur la méthode Kaizen qui regroupe 10 états d’esprits :
- La remise en question permanente.
- Priorisez les bonnes idées et les changements.
- Corrigez les erreurs rapidement et prenez le temps de faire bien du premier coup.
- Soyez proactif, anticipez et prenez des initiatives.
- Cherchez la durabilité dans la mise en place de vos actions.
- N’ayez pas peur, les difficultés et contraintes sont sources de progrès.
- Cherchez la cause du problème à sa source (5 pourquoi) et résolvez-la.
- Interrogez : plusieurs idées différentes valent mieux qu’une seule.
- Évitez de gaspiller pour mieux optimiser.
- Appuyez-vous sur des méthodes qui ont fait leur preuve : Méthode PDCA (Plan, Do, Check, Act), les 5S (Seiri, Seiton, Seiso, Seiketsu, Shitsuke), les 5 pourquoi.
Pour conclure, l’amélioration continu est basé sur plusieurs principes :
- La remise en question permanente :
Accepter de ne pas toujours avoir raison.
- La priorité sur les changements :
Accepter que les habitudes soient chamboulés.
- La correction rapide des erreurs :
Trouver immédiatement une solution aux problèmes.
- La proactivité :
Essayer d’anticiper tous les problèmes possibles.
- La durabilité des actions :
Mettre en place des actions durables.
- La réduction du gaspillage :
Chercher à supprimer toute forme de déchets inutiles.
- L’écoute :
Prendre le temps de discuter, d’échanger avec ses collaborateurs.